Unlock your paper box design skills and become an industry expert with this must-read article. Don’t wait any longer, dive in now!
Finalize your product’s packaging design with @klong-packaging!
Packaging is the first point of contact between your product and customers, making it a vital aspect of your brand. With almost three decades of experience, we provide top-notch paper packaging solutions to help your product stand out on the shelf, catch the eye, and effectively communicate your message.
In this blog post, learn about material choices, printing methods, artwork design, and coating methods to design the perfect color box that will sell more of your products.

Part I: Material Selection List
Choose from a wide range of options including corrugated color boxes, single paper boxes, and rigid-chipboard boxes. Each option has its own advantages and considerations based on your product’s size and weight.
- Corrugated color box: The surface paper is mostly made of 250~400gsm CCNB, kraft paper, SBS, etc. The wave paper depends on the size and weight of the product, and the commonly used ones are 2-layer or 3-layer F-flute, E-flute, and B-flute.
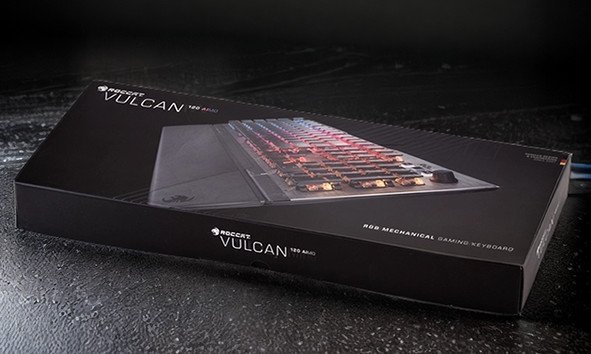
- Single paper boxes, mostly SBS (easy to print and surface coating treatment), Between 250 ~ 400g with a thickness of about 0.30 ~ 0.55mm. Here please note that the choice of this option, either your product is very light, or inside must be added to the insert or tray to protect the product.
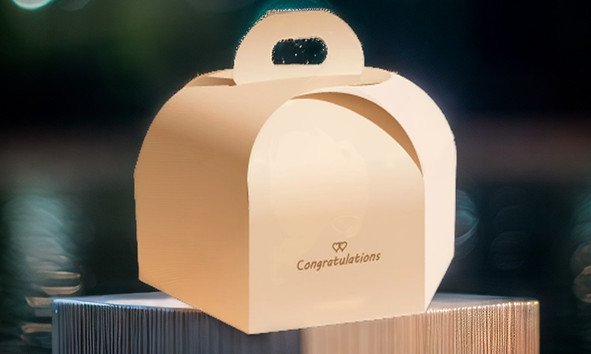
- Rigid cardboard box, the box is harder, and molding thickness is usually between 1.0~3.0mm, also, the cost is higher. Most of the cardboard is 600g~1800g. The outer wrap paper is mostly 128g ~ 157g C2S. Of course, you can also use a thick one to do this, but in this case, the outer paper needs to be slotted, due to the cost of thicker outer paper and the process increases, the corresponding cost is also higher than usual.
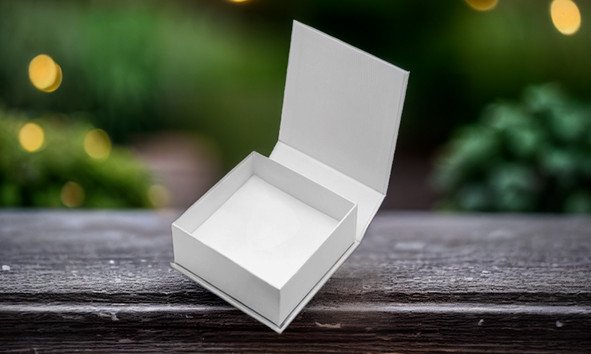
Part II: Printing Method Selection
The printing method you choose will greatly impact the overall effect of your color box design. We mainly offer offset printing, flexographic printing, and silkscreen printing to ensure your design looks its best.
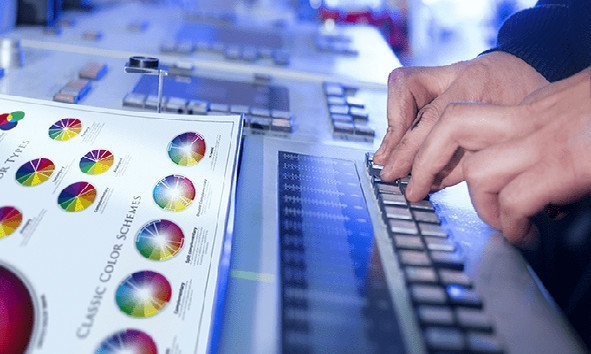
- Offset printing is the most common printing method because it can accurately print large areas with solid colors and various details.
- Flexo printing is mostly used for corrugated boxes.
- Silkscreen printing is mostly used for printing on paper that is not easy to ink such as kraft paper and other special paper. The advantage is that the text is very clear, the disadvantage is that the content can not be complex, mostly for single texts or some brand logos and slogans.
Part III: Artwork Design Suggestions
It should be clear and concise, but also effective in conveying information to the audience.
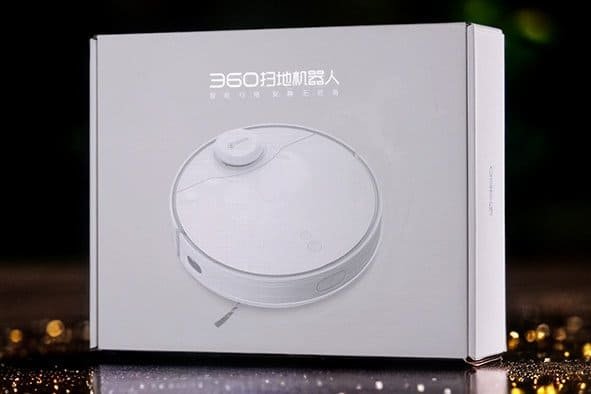
At Klong-packaging, we strongly recommend:
- keeping text to a minimum.
- emphasizing the brand name, product name, and any important information.
- Use font sizes and styles that are clear and easy to read, and make sure that the font color is sufficiently contrasting with the background color to make it easy to read.
- Also consider the language used, keeping the target audience in mind and avoiding any words that could cause confusion or misunderstanding.
Part IV: Coating & Varnishing Method
Enhance your color box with varnishing options such as oil and lamination.
You can also choose spot UV, foil stamping, embossing, or debossing to highlight specific elements.
Our experts will help you find the perfect balance for your design.
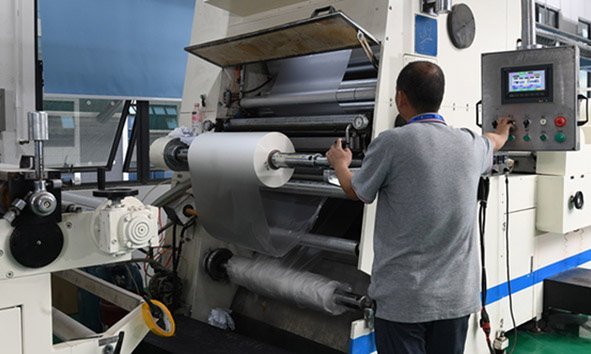
In conclusion, the design of your color box is crucial in shaping customers’ perception of your product. Trust klong-packaging to provide quality, functional, and visually pleasing paper packaging solutions.
Contact us today to bring your ideas to life.